What should you check for when inspecting a crane before maintenance?
What are some things to remember when repairing a crane?
What should you check for when inspecting a crane before maintenance?
- Lower hoist to unload rope sheaves.
- Unwind all wire rope from the hoist drum to expose all parts of a rope, making sure that the rope does not rewind in the reverse direction.
- Inspect sheaves, sockets, dead-ends, thimble joints, and all wire rope hardware.
- During rope changes, check the sheaves for worn bearings, broken flanges, proper groove size, smoothness, and contour.
- Inspect all parts of the cable, cleaning wire rope only as required to complete an inspection. Excessive removal of lubrication will lead to damage.
- Re-lubricate rope to prevent corrosion, wear, friction, and drying out of the core.
- Check for ropes that may have been operated dry (unlubricated). Replace dry ropes. There may be hidden damage that is not detected by visual inspection.
- Compare the rope length and diameter with the original dimensions. Lengthening accompanied by diameter reduction is often an indication of interior core defects.
- Visually examine the crane structure for deformed, cracked or corroded members in the structure and boom. Check for loose bolts or rivets. Check for excessive wear on brake and clutch system parts.
- Check for deterioration or leakage in air or hydraulic systems.
- Check all control mechanisms for poor adjustment or excessive wear.
- Check accuracy of marking on the load/radius indicator over full range.
- Establish a schedule of rope replacement to change wire rope before it breaks. Periodic replacements do not take the place of inspections. If rope breaks or inspections reveal abnormal wire breakage or defects, reduce the time between replacement. Do not make wire rope slings from used wire rope.
What are some things to remember when repairing a crane?
- Take a crane to a location where repairs will least interfere with other cranes.
- Ensure that all controllers are placed in the "off" position, and the main switches are open and locked.
- Place on the switch a standard warning tag stating "DO NOT START." The tag must be filled out and signed
- Place rail stops or make other safety provisions when another crane operates on the same runway.
- Use fall protection equipment.
- Do not carry anything in your hands when going up and down ladders. Items that are too large to go into pockets or belts should be lifted to or lowered from the crane by a rope.
- Prevent loose parts or tools from falling to the floor.
- The area below the crane must be cleared and a barrier erected to prevent injury from a falling object.
- Replace all guards and other safety devices before leaving a crane.
- Remove all stops, tools, loose parts and other material and dispose of them before completing the repair job.
- Enter all service inspections and repairs in a crane log book or file
Hoist Wire Rope
Who should inspect wire ropes and when?
When should you eliminate the rope from its use?
What can cause a wire rope break?
Who should inspect wire ropes and when?
- Only trained personnel should carry out an inspection of wire ropes.
- Inspect a wire rope when installing it.
- Inspect wire ropes every working day.
- Keep records of daily inspections.
- Check for abrasions, corrosion, pitting, and lubrication inside rope. Insert a marlin spike beneath two strands and rotate to lift strands and open rope.
When should you eliminate the rope from its use?
Assess the condition of the rope at the section showing the most wear. Discard a wire rope if you find any of the following conditions:
- In running ropes (wound on drums or passed over sheaves), 6 or more broken wires in one lay length; 3 or more broken wires in one strand in one lay.
- In pendant standing ropes, 3 or more broken wires in one lay length.
- Wear of 1/3 of the original diameter of individual outside wires.
- Kinking, crushing, cutting or unstranding, bird caging or other physical damaged that has distorted the shape of the wire rope.
- Heat damage (check for burn marks, discoloration of the metal).
- Excessive stretch or sharp reduction in the rope diameter.
- Knots or splices (except eye splices) in a wire rope.
What can cause a wire rope break?
- Wear on areas in contact with hoist sheaves and drums.
- Corrosion from lack of lubrication and exposure to heat or moisture (e.g., wire rope shows signs of pitting). A fibre core rope will dry out and break at temperatures above 120°C (250°F).
- Fatigue from repeated bending even under normal operating conditions.
- Overloading the safe working load limit. Follow manufacturers' charts.
- Mechanical abuse - crushing, cutting or dragging of rope.
- Kinks from improper installation of new rope, sudden release of a load or knots made to shorten a rope. A kink cannot be removed without creating a weak section. Discarding kinked rope is best.
|
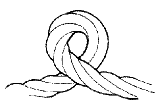
|
|
|